1 引言
目前產(chǎn)品的競爭, 尤其是家用電器產(chǎn)品的競爭越來越激烈, 如何縮短產(chǎn)品的開發(fā)周期, 及時推出適合市場的新產(chǎn)品成為各大公司共同關(guān)心的問題。Pro/E軟件以其強大的造型及結(jié)構(gòu)設(shè)計功能在產(chǎn)品的開發(fā)設(shè)計中得到越來越廣泛的應(yīng)用, 為有效縮短產(chǎn)品的開發(fā)周期提供了條件。積水盤是壁掛空調(diào)器的主要部件,是由復(fù)雜的外形特征組成, 其設(shè)計的好壞將直接影響到空調(diào)器的積水效果、裝配性能和產(chǎn)品內(nèi)在質(zhì)量等要素。通過利用Pro/E Wildfire2.0軟件進行積水盤的三維數(shù)據(jù)模型設(shè)計、澆注系統(tǒng)設(shè)計、分模設(shè)計及裝配設(shè)計和冷卻系統(tǒng)設(shè)計等, 不僅縮短了模具的設(shè)計及制造周期,提高了模具的質(zhì)量和使用壽命, 而且還增加了模具的潛在價值和市場競爭力, 為新產(chǎn)品迅速占領(lǐng)市場打下了堅實的技術(shù)基礎(chǔ)。
2 積水盤產(chǎn)品設(shè)計
2.1 接受任務(wù)書
成型塑料制件的任務(wù)書通常由制件設(shè)計者提出,其內(nèi)容如下:
( 1) 過審簽的正規(guī)制件圖紙, 并注明采用塑料的牌號、透明度等。
( 2) 塑料制件說明書或技術(shù)要求。
( 3) 生產(chǎn)產(chǎn)量。
( 4) 塑料制件樣品。
通常模具設(shè)計任務(wù)書由塑料制件工藝員根據(jù)成型塑料制件的任務(wù)書提出, 模具設(shè)計人員以成型塑料制件任務(wù)書和模具設(shè)計任務(wù)書為依據(jù)來設(shè)計模具。
2.2 設(shè)計依據(jù)分析
該模具設(shè)計的依據(jù)是塑件圖紙和塑料制件樣品。
對于塑件圖紙, 要注意圖紙的技術(shù)要求, 許多圖紙明確給出尺寸公差等級、未注圓角、產(chǎn)品壁厚等, 這些在模具設(shè)計時必須加以注意; 對于塑料制件樣品, 重點是在樣件上提取有用的模具設(shè)計信息, 避免在設(shè)計上走彎路, 這些信息包括分型面的位置、澆口的位置和形式、頂桿的大小與分布、抽芯機構(gòu)的設(shè)計等等。
該塑件材料為塑料ABS, 制件顏色為乳白色, 按統(tǒng)一色板檢驗, 色澤為1008。制件成型后要求外觀挺括, 無明顯縮印、裂紋、流痕、熔接痕、頂白、銀絲斑、冷夾、劃傷、擦毛等缺陷, 澆口、頂桿痕及分型合模線等飛邊毛刺應(yīng)修邊完整干凈, 不得損傷外觀。尺寸公差按GB/T14486- 93 標準MT2 級執(zhí)行, 內(nèi)外表面粗糙度為Ra3.2!m, 壁厚為2.5mm, 未注倒圓角為R0.5mm,訂貨要求采用1 模1 腔, 模具壽命為50 萬模次。
2.3 消化塑料制件圖和工藝資料
設(shè)計人員要認真消化圖紙, 了解制件的用途, 分析塑料制件的工藝性, 尺寸精度等技術(shù)要求。例如塑料制件在外表形狀、顏色透明度、使用性能方面的要求是什么, 塑件的幾何結(jié)構(gòu)、斜度、嵌件等情況是否合理, 熔接痕、縮孔等成型缺陷的允許程度, 有無涂裝、電鍍、膠接、鉆孔等后加工。選擇塑料制件尺寸精度最高的尺寸進行分析, 看看估計成型公差是否低于塑料制件的公差, 能否成型出合乎要求的塑料制件來。此外, 還要了解塑料的塑化及成型工藝參數(shù)。消化工藝資料, 分析工藝任務(wù)書所提出的成型方法、設(shè)備型號、材料規(guī)格、模具結(jié)構(gòu)類型等要求是否恰當, 能否落實。
成型材料應(yīng)當滿足塑料制件的強度要求, 具有好的流動性、均勻性和各向同性、熱穩(wěn)定性。根據(jù)塑料制件的用途, 成型材料應(yīng)滿足染色、鍍金屬的條件、裝飾性能、必要的彈性和塑性、透明性或者相反的反射性能、膠接性或者焊接性等要求。
2.4 零件三維建模
積水盤材料為ABS 塑料,注射加工成型。其形狀大體為細長形,由兩端復(fù)雜曲面、加強筋、勾卡等特征組成,采用Protrusion( 伸出項) 、Cut( 切減項) 、Rib( 加強筋) 、Round ( 倒圓角) 、Offset ( 偏移) 、Curve ( 曲線) 、Surface ( 曲面) 、Surface Merge ( 曲面合并) 、SurfaceExtension ( 曲面延長) 、Transformed Surface ( 鏡像) 、Draft( 拔模) 等實體特征和曲面特征完成積水盤的三維數(shù)據(jù)建模。其簡要建模步驟如下:
( 1) 建立基準面和基準坐標系。
( 2) 建立積水盤外形特征( 使用Protrusion、Cut、Offset、Round、COPIED_GROUP、Curve、Surface、SurfaceMerge、Surface Extension、Transformed Surface、Draft等命令) 。
( 3) 建立柱子、溝槽等部分細節(jié)特征( 使用Protrusion、Cut、Offset、Round、COPIED_GROUP、Surface、Surface Merge、Surface Extension、Draft等命令) 。
( 4) 建立勾卡特征( 使用Protrusion、Cut、Round、COPIED_GROUP、Curve 等命令) 。
( 5) 建立積水盤的加強筋特征(Rib、Round) 。
( 6) 加未注脫模斜度1°特征(Draft) 。
( 7) 倒未注圓角R0.5mm(Round) 。
( 8) 對產(chǎn)品進行渲染。最后完成的積水盤三維數(shù)據(jù)模型如圖1 所示。
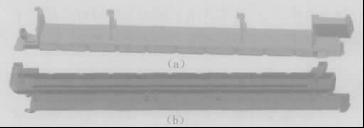
圖1 積水盤三維模型
a—— 正面b——反面
3 模具結(jié)構(gòu)設(shè)計
3.1 建立分模文件、裝配參考零件(Ref Model) 、創(chuàng)建工件(Workpiece )
Create a new object→在Component Creat 對話框中, Type 欄選Manufacturing, sub - type 欄選MoldCavity, 輸入文件名kfr35gt- jsp- mold, 點OK 按鈕確定。Mold Model →Assemble →Ref Model →openkfr35gt- jsp.prt→在Component Placement 對話框中點缺省按鈕(Assemble component at default location) →再點OK 按鈕即可。Mold Model →Create →Workpiece →Manual → 輸入工件名稱kfr35gt - jsp -wrk→Create features→OK→protrusion, 根據(jù)積水盤的最大外形尺寸先創(chuàng)建出一個稍大于積水盤的工件即可, 因為在進行后續(xù)斜導(dǎo)柱滑塊設(shè)計時需根據(jù)滑塊的大小來最終決定動、定模芯的大小。
3.2 拔模斜度及厚度檢測
為了避免在隨后的設(shè)計中產(chǎn)生不必要的失誤和少走彎路, 在建立分型面前必須對參考零件(RefParts) 進行拔模斜度和厚度檢測, 看是否有倒勾(Untercut) 、拔模斜度不合理或零件厚度嚴重不均等現(xiàn)象。若存在就要修改零件模型, 有時候甚至要修改零件模型的部分結(jié)構(gòu), 直到消除所有該類現(xiàn)象為止。但是必須注意在進行分模設(shè)計前最好先將造型好的零件模型請客戶過來確認, 看修改的地方會不會影響外觀、裝配性能等。因為若你一開始就不注意這些問題,當你送樣件給客戶確認時, 客戶可能提出很多修改要求( 包括在零件模型分析后進行修改的地方以及客戶沒有考慮到的地方) 。這樣就會增加很多后續(xù)改模工作, 既浪費了寶貴的時間, 也增加了模具的制造成本。
3.3 設(shè)置收縮率( 0.5%)
Shrinkage →By Dimension →Set/Reset →AllDims →Enter shrink ratio 'S' ( Formula:1 +S) for alldimensions: 0.005→Done Scale。
3.4 澆注系統(tǒng)設(shè)計
澆注系統(tǒng)的作用是將熔融狀態(tài)的塑料填充到型腔內(nèi), 并在填充的過程中將注射壓力傳遞到塑件各部位,從而得到所需的塑件。澆注系統(tǒng)一般由澆口、流道、進料口、冷料井四部分組成。本模具設(shè)計采用4個點澆口進料, 澆口隨二次分型時自動脫落,這樣既節(jié)約了生產(chǎn)時間,又提高了勞動生產(chǎn)效率。該澆注系統(tǒng)是在Pro/E塑料顧問選件中建立的, 通過在流動分析過程中不斷調(diào)整澆口位置、數(shù)量及大小來優(yōu)化流道系統(tǒng), 最終得到如圖2所示的最佳澆注系統(tǒng), 在這里就不再贅述。
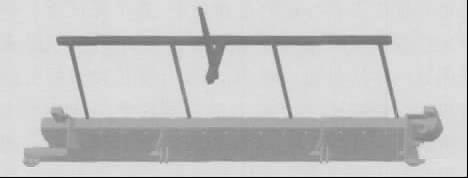
圖2 積水盤澆注系統(tǒng)
3.5 建立分型面( Parting Surface )
由于積水盤形狀復(fù)雜, 其模具結(jié)構(gòu)設(shè)計就更為復(fù)雜, 因此主分型面設(shè)計的好壞直接影響到相關(guān)成型零件設(shè)計與加工的難易程度, 甚至會影響到整副模具的使用壽命。為此, 在綜合考慮結(jié)構(gòu)設(shè)計合理和加工方便等要素的前提下最后設(shè)計出如圖3 所示的主分型面。其簡要操作步驟為: Parting Surface→Creat→輸入分型面名稱( 如Parting_Surface01) →Add→根據(jù)零件幾何形狀通過采用Copied_Group、Surface、SurfaceMerge、Surface Extension、Transformed Surface 等命令來完成主分型面的創(chuàng)建。
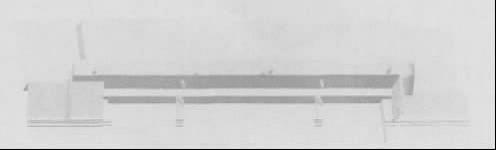
圖3 積水盤主分型面
3.6 分模
Mold Volum →Split → 選取分型面( PartingSurface) →分割出動、定模芯。接著使用Mold Volum→Create, 輸入要建立的鑲件的名稱, 如dongm- huak01、dingm- huak01 與xietui1234 等, 建立如圖4 所示的5個滑塊和4 個斜推。然后抽取出動、定模芯(MoldComp→Extract) →生成澆注件(Molding) →根據(jù)生成的各滑塊和斜推對動、定模芯進行優(yōu)化設(shè)計→開模(Mold Opening) , 如圖5 所示。最后再次進行拔摸檢測, 看是否存在倒勾現(xiàn)象, 若有就必須進行相應(yīng)修改,直到消除所有倒勾為止。在創(chuàng)建圖5 中定模側(cè)的兩滑塊組件時, 必須特別注意每組滑塊之間的運動方向和形式, 由于采用滑塊套滑塊的方式, 其動作的穩(wěn)定性就顯得尤為重要, 既要保證開模時斜導(dǎo)柱滑塊能順利抽芯, 同時又得保證在閉模時每個滑塊組件能順利回復(fù)到位。在進行每組滑塊設(shè)計時必須清楚它們各自的運動角度以及斜導(dǎo)柱的運動角度, 為了保證運動平穩(wěn)決定在脫澆板與定模板之間加4 個復(fù)位彈簧, 經(jīng)實踐證明這一舉措是很正確的, 若沒有復(fù)位彈簧就會經(jīng)常造成斜導(dǎo)柱咬死、拉毛以及斷裂等現(xiàn)象。另外動模側(cè)3個滑塊按照常規(guī)方法去進行結(jié)構(gòu)設(shè)計即可, 但必須注意中間的大滑塊為了產(chǎn)品能順利出模, 不是在水平面內(nèi)運動, 而是在與水平面成一小角度的斜面上運動,故在設(shè)計斜導(dǎo)柱時必須特別注意這一點。
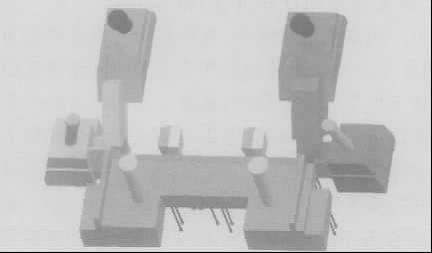
圖4 滑塊與斜推
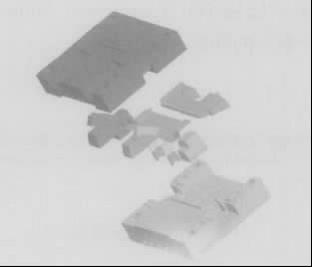
圖5 積水盤分模
3.7 模架裝配與零部件結(jié)構(gòu)設(shè)計
使用Pro/ASSEMBLY 裝配模塊創(chuàng)建的三維注射模架, 該模架為三板式細水口系列模架, 模架最大外形尺寸為1250×750×700 ( 單位: mm) , 擬選用海天HTF760X 型注射機。同樣在Pro/ASSEMBLY 裝配模塊中創(chuàng)建各相關(guān)零部件的三維模型, 并不斷進行結(jié)構(gòu)優(yōu)化設(shè)計, 以保證各零部件不僅加工簡單方便, 而且模具動作也靈活自如。在繪制完所有相關(guān)零部件后, 使用菜單欄中的Analysis 進行全局干涉檢查(MoldAnalysis→Global interference→Compute) , 對有干涉的地方及時進行修改與優(yōu)化, 直到?jīng)]有任何干涉為止。
3.8 冷卻系統(tǒng)設(shè)計
塑料充滿型腔后, 應(yīng)通過冷卻使之定型, 從而得到所需制品。冷卻水道的位置分布應(yīng)遵循一定的原則, 總的來說, 應(yīng)保證塑件充分冷卻且收縮平衡, 而又不與其它零部件、孔系發(fā)生連通現(xiàn)象, 以免漏水。本例中動、定模水道均采用縱向排布, 直徑均為φ10mm, 采用Pro/ASSEMBLY 裝配模塊中的Cut 命令來完成水道孔的設(shè)計, 其具體布置形式見圖6。冷卻系統(tǒng)設(shè)有翻水孔, 以增加冷卻效果, 同時采用O 型密封圈密封, 以免出現(xiàn)泄漏現(xiàn)象, 而且冷卻管接頭不要露在模具外面,以免吊裝和放置模具時將其壓壞。
最后使用Mold Analysis 中的Assembly MassProperties 進行重量計算, 結(jié)果為3.9t。最終生成的三維模具裝配圖如圖6 所示。
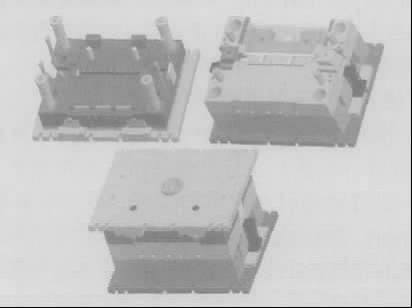
圖6 積水盤三維模具圖
4 結(jié)束語
由于塑料制件的結(jié)構(gòu)越來越復(fù)雜, 帶來模具的結(jié)構(gòu)也越來越復(fù)雜, 這就要求我們模具設(shè)計人員不斷地想出更多合理可靠的模具結(jié)構(gòu)來成型不同要求的制件。在實際的設(shè)計工作中, 我們應(yīng)充分利用我們所掌握的有關(guān)數(shù)學、力學以及材料學等相關(guān)方面的知識, 通過運用國內(nèi)外先進的CAD/CAE/CAM集成技術(shù)軟件來進行模具結(jié)構(gòu)設(shè)計與開發(fā)工作, 這樣我們就會不斷提高自身的業(yè)務(wù)技能和專業(yè)水平, 從而增加新產(chǎn)品的潛在價值和市場競爭力, 為企業(yè)帶來了良好的經(jīng)濟效益。